Prospective projects
The National Research and Development Institute for Gas Turbines COMOTI is currently engaged into developing a new, breakthrough, high speed propulsion technology based on the principle of pulsed detonating combustion.
The central idea of the investigated propulsion technology is the replacement of the gas turbine in a typical aviation engine of today by a simpler, and at least as effective system. The advantages of the approach are multiple. Firstly, the gas turbine represents about 25 % of the total weight of the engine, so, its replacement by a simpler system will lead to a decrease in engine weight. Secondly, the most important limitations for the modern gas turbine engines are related to the maximum temperature at the turbine inlet. As the turbine blade material can only withstand a certain maximum temperature, in order to maximize the temperature of the burned gas at the combustor exhaust, and therefore the performances of the engine, the turbine blades, especially for the first rows, need to be cooled. Given the dimensions and the complex geometry of the typical turbine blade, the design and machining of the cooling channels to and through the blades is a difficult and expensive process. The replacement of the turbine by a simpler power device would, therefore, simplify the design and the manufacturing of the engine and lower its costs. Thirdly, a gas turbine is a very complex machine, including a large number of rotating parts subjected to high temperature, and typically made from expensive and hard to machine materials. A simpler power device would lower significantly the time and the costs allocated to design, manufacturing and maintenance, while reducing the failure risks in both manufacturing and exploitation by reducing the number of parts. Finally, the dimensions of the engine, particularly its length, can also be reduced by replacing a series of turbine disks and stators by a more compact solution.
The concept uses the conservation of impulse for the combustor exhaust jet released tangentially, to rotate the entire combustor assembly. The combustor assembly contains several can combustors rotating together and connected together through a disk to a central shaft and enclosed in a stationary pressurized shroud. The shaft of the combustor assembly is connected, and provides power, to a compressor upstream of the combustor that provides pressure to the combustor shroud. The remaining energy will be used to power the aircraft. The typical approaches to extract this energy are via a propeller connected, possibly through a gear box, to the main shaft, via a main exhaust nozzle that collects the flow from the combustors re-axialize it, and accelerates it to provide reactive thrust, or via a combination of the two. If the propeller solution is used, like in a turboprop, after the momentum transfer to the rotating combustor assembly, the low kinetic energy, high pressure jet is collected into an exhaust chamber, connected to a nozzle that further extracts the potential energy from the burned gas, providing additional thrust for the aircraft, such that a full expansion of the exhaust gas is achieved. The solution has the disadvantage of requiring the addition of a gearbox, to match the optimal propeller speed and the speed of the compressor and of the rotating combustor disk. If the reactive nozzle solution is preferred, like in a turbojet, the losses incurred through the re-axialization of the flow are higher. To diminish them, the fraction of the energy transferred to the shaft can be controlled through the shape of the rotating combustor nozzles, and the direction of the jet exiting the combustors. Thus, as the jet direction is closer to the axial direction, the tangential impulse transmitted to the central shaft decreases, up to a point where only the energy required to balance the compressor work is converted into rotational speed. The remaining energy, both potential (pressure) and kinetic (velocity) is extracted from the flow by means of the engine exhaust nozzle.
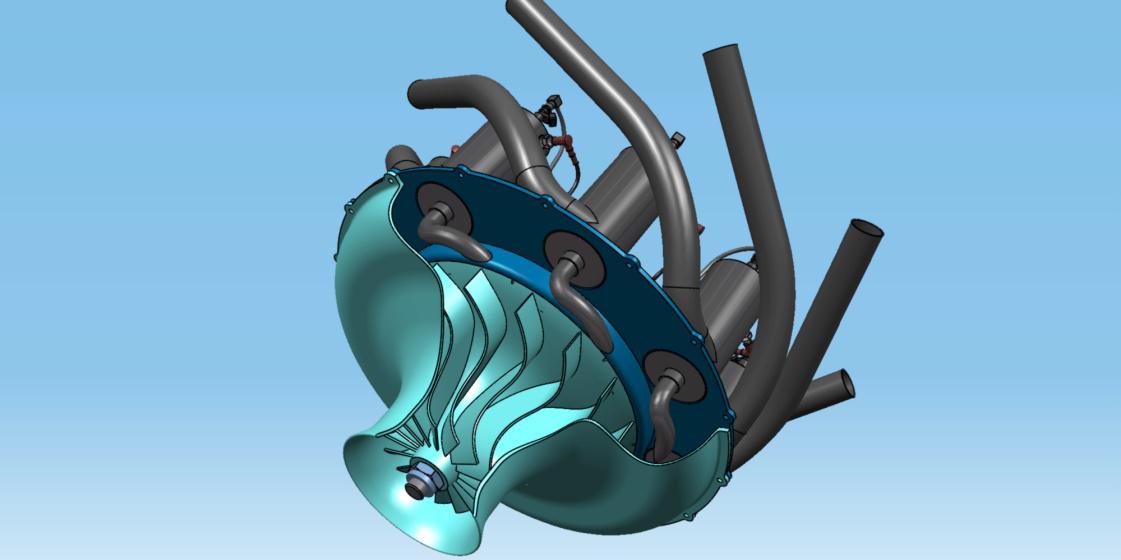